What is the use of medical plastic injection molding?
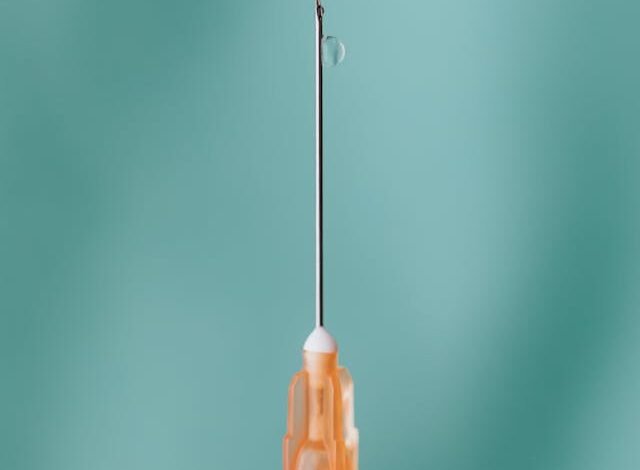
Medical plastic injection molding is a crucial process in the manufacturing of various medical devices, instruments, and packaging materials. It enables the production of intricate and precise components that play a significant role in healthcare delivery. Let’s delve deeper into the significance and applications of medical plastic injection molding.
Introduction to Medical Plastic Injection Molding
Medical Plastic Injection Molding is a specialized manufacturing process used to produce intricate and precise plastic components for medical applications. This process involves injecting molten plastic material into a mold cavity under high pressure, where it cools and solidifies to form the desired shape.
Understanding the Process
Injection Molding Basics
The process begins with the feeding of plastic pellets into the injection molding machine’s hopper, where they are heated and melted. The molten plastic is then injected into a mold cavity, which is usually made of steel or aluminum. Once the plastic cools and solidifies, the mold opens, and the finished part is ejected.
Materials Used
Medical-grade plastics such as polyethylene, polypropylene, polycarbonate, and thermoplastic elastomers are commonly used in medical injection molding due to their biocompatibility and sterilization capabilities.
Importance of Precision
Precision is crucial in medical plastic injection molding to ensure that the manufactured components meet the stringent requirements of medical devices and instruments. Tight tolerances and accurate dimensions are essential to maintain the functionality and safety of these products.
Applications in the Medical Field
Medical plastic injection molding finds widespread applications across various sectors of the healthcare industry, including:
Medical Devices
Medical devices such as syringes, catheters, tubing, and connectors are often manufactured using plastic injection molding. These components require high precision and reliability to perform their intended functions effectively.
Surgical Instruments
Many surgical instruments, including forceps, scalpels, and retractors, are made using medical plastic injection molding. The process allows for the production of lightweight and ergonomic instruments that offer superior performance and durability.
Pharmaceutical Packaging
Plastic containers, vials, and packaging materials used in pharmaceutical applications are often produced through injection molding. These packaging solutions must meet strict quality standards to ensure the integrity and safety of pharmaceutical products.
Advantages of Medical Plastic Injection Molding
Customization
Medical plastic injection molding enables the customization of components to meet specific design requirements and functionalities. Manufacturers can easily modify molds and production processes to accommodate changes in product design or specifications.
Cost-effectiveness
Despite the initial tooling costs, medical plastic injection molding offers long-term cost savings due to its high production efficiency and repeatability. Mass production capabilities and minimal material waste contribute to overall cost-effectiveness.
Sterilization Compatibility
Plastic materials used in medical injection molding are compatible with various sterilization methods such as autoclaving, gamma irradiation, and ethylene oxide. This ensures that medical devices and instruments remain sterile and safe for use in clinical settings.
Quality Assurance and Regulatory Compliance
ISO Standards
Manufacturers of medical plastic components must adhere to stringent quality standards outlined by organizations such as the International Organization for Standardization (ISO). Compliance with ISO 13485 ensures that the manufacturing process meets the highest quality management system requirements for medical devices.
FDA Regulations
In the United States, medical plastic injection molding facilities must comply with regulations set forth by the Food and Drug Administration (FDA). FDA oversight ensures that medical devices and components meet safety and efficacy standards before they are introduced to the market.
Sustainability Considerations
Material Selection
The selection of sustainable and environmentally friendly materials is gaining importance in medical plastic injection molding. Manufacturers are exploring biodegradable and recyclable plastics to reduce environmental impact and promote sustainability.
Waste Reduction
Efforts to minimize waste generation and optimize manufacturing processes are essential in medical plastic injection molding. Recycling initiatives and efficient material usage contribute to reducing the industry’s carbon footprint and conserving resources.
Future Trends and Innovations
Advanced Materials
Advancements in material science are driving the development of new and improved plastics for medical injection molding. Biocompatible polymers, nano-materials, and bioresorbable polymers are among the innovative materials poised to revolutionize the healthcare industry.
3D Printing Integration
The integration of 3D printing technologies with traditional injection molding processes holds immense potential for enhancing product development and customization in the medical field. Additive manufacturing enables rapid prototyping and the production of complex geometries with minimal material waste.
Conclusion
Medical Plastic Injection Molding plays a vital role in the production of medical devices, instruments, and packaging materials. Its ability to produce customized, cost-effective, and sterilization-compatible components makes it indispensable in the healthcare industry. As technology continues to advance, we can expect further innovations in materials, processes, and sustainability practices to drive the evolution of medical plastic injection molding.