How to Choose Rivet Fasteners for High-Temperature Applications
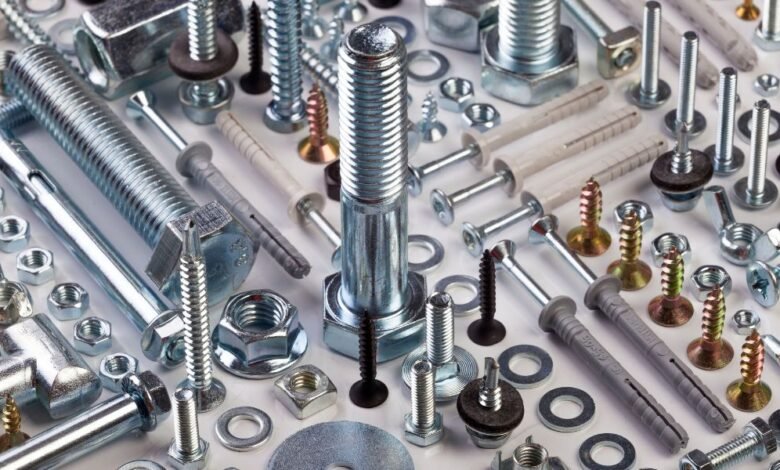
Are you looking for the best rivet fasteners for high-temperature applications? Selecting the right fastener is essential for maintaining the structural integrity of materials exposed to extreme heat. This is especially critical in industries like aerospace, automotive, and manufacturing, where rivets need to be strong, durable, and heat-resistant.
Choosing rivet fasteners for high-temperature environments involves evaluating several factors, such as material properties, strength, and heat resistance. A rivet nut, for instance, is an ideal option for creating secure threaded connections in high-stress applications. Understanding these aspects can guide you in selecting the right rivet fastener for your needs.
Material Selection for High-Temperature Rivets
The material used for these fasteners is a key factor when selecting the right option for high-temperature applications. Common materials such as stainless steel, titanium, and specialized alloys are ideal because they provide strength and heat resistance. These materials can endure the thermal expansion and contraction that high temperatures cause, ensuring the fasteners perform well under stress.
Stainless steel is widely used for its corrosion resistance and strength. Titanium, while more expensive, offers excellent heat resistance and durability. For extremely high temperatures, specialized alloys provide the necessary performance to withstand demanding conditions. Be sure to select a material that matches the maximum temperature your application will experience.
See also: Unlocking the Power of Zulu Muscle: Traditional Strength Training Techniques
Strength and Durability of Rivet Fasteners
Strength and durability are essential when choosing rivet fasteners. The rivet must securely hold components under stress from vibrations, thermal cycling, and heavy loads. Tensile and shear strength are critical measures to ensure that these will maintain its integrity in high-heat environments.
Another important consideration is fatigue resistance. High temperatures and constant stress can weaken materials over time. Rivets with high fatigue resistance will last longer and remain reliable in high-stress applications. Consider how well the material will perform when exposed to continuous heat cycles and pressure.
Types of Rivet Fasteners for High-Temperature Environments
There are various types of rivet fasteners that can be used in high-temperature applications. Depending on the needs of the application, each type has unique benefits. Blind rivets, solid, and rivet nuts are some of the most commonly used options.
They are particularly beneficial when you need a strong, threaded connection in thin materials. They are ideal for applications that require frequent assembly and disassembly. This feature makes them suitable for environments where high-temperature resistance and repeated reassembly are necessary.
Corrosion Resistance and Coatings
In high-temperature environments, exposure to corrosive elements like moisture and chemicals is common. This can accelerate oxidation and lead to the deterioration of these fasteners. As a result, corrosion resistance is essential in these applications.
To combat corrosion, rivets are often coated with protective layers such as zinc plating, anodizing, or high-heat resistant coatings. These coatings help protect it from moisture and chemicals while maintaining its structural integrity. When working in environments exposed to harsh conditions, it’s vital to ensure the coatings will remain effective at high temperatures.
Ensuring Easy Installation and Maintenance
Ease of installation and maintenance is another factor to consider when selecting rivet fasteners. Fasteners that are easy to install reduce labor costs and improve efficiency, particularly in manufacturing environments where downtime can be costly.
Rivet nuts are especially useful for applications that require disassembly and reassembly, as their threaded design makes the process simpler. This feature ensures that maintenance can be performed quickly without damaging surrounding materials. The ability to service components without full disassembly or causing damage is one of the key advantages of them in high-temperature applications.
When choosing rivet fasteners for high-temperature applications, material selection, strength, durability, and ease of maintenance are crucial factors to consider. A rivet nut, with its reliable threaded connection, offers excellent performance in high-heat environments. By carefully selecting the right fasteners, you can ensure the long-term reliability and security of your high-temperature applications.