What Does Medical Plastic Injection Molding Mean?
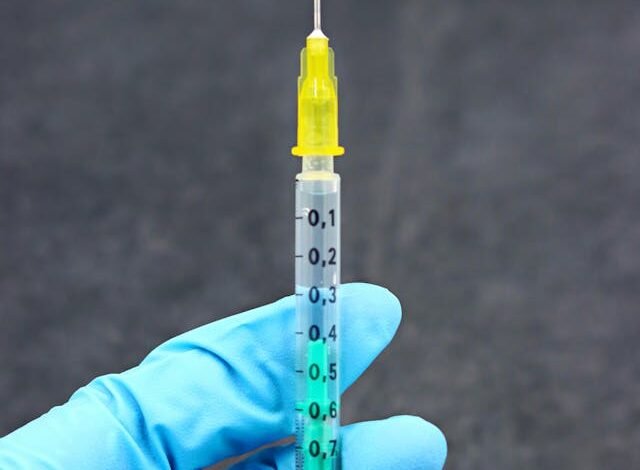
Medical plastic injection molding is a crucial process in the healthcare industry, involving the production of intricate and precise plastic components used in medical devices, equipment, and instruments. This article explores the significance, process, applications, regulatory aspects, advancements, benefits, challenges, and sustainability of medical plastic injection molding.
Introduction to Medical Plastic Injection Molding
In the realm of healthcare, precision and quality are paramount. Medical Plastic Injection Molding ensures the production of high-quality plastic components that meet the stringent standards of the medical industry. This process has revolutionized the manufacturing of medical devices and equipment, offering unparalleled precision and reliability.
Understanding Plastic Injection Molding
Basics of Injection Molding
Plastic injection molding is a manufacturing process wherein molten plastic is injected into a mold cavity under high pressure. Once cooled and solidified, the mold is opened, and the final product is ejected. This process is highly versatile and is used across various industries due to its efficiency and cost-effectiveness.
Importance of Plastic in the Medical Industry
Plastic materials play a vital role in the medical field due to their versatility, durability, and biocompatibility. Medical-grade plastics are extensively used in the production of implants, surgical instruments, diagnostic equipment, and packaging materials.
Significance of Medical Plastic Injection Molding
Precision and Accuracy
Medical plastic injection molding offers unmatched precision and accuracy, ensuring that each component meets the exact specifications required for its intended purpose. This level of precision is crucial in medical applications where even the slightest deviation can have serious consequences.
Cost-effectiveness
Despite the initial setup costs, medical plastic injection molding proves to be highly cost-effective in the long run. The ability to mass-produce intricate components with minimal waste reduces manufacturing costs and enables economies of scale.
Material Selection
The choice of material is critical in medical plastic injection molding to ensure compatibility with regulatory standards, biocompatibility, sterilization methods, and durability. Common materials include polyethylene, polypropylene, polycarbonate, and thermoplastic elastomers.
Process of Medical Plastic Injection Molding
Medical plastic injection molding involves several distinct steps to produce high-quality medical components.
Mold Designing
The process begins with the design and fabrication of a mold that matches the desired specifications of the final product. Factors such as geometry, surface finish, and material selection are carefully considered during the mold design phase.
Material Preparation
The selected plastic material is then prepared by melting it to a precise temperature suitable for injection molding. Additives may be incorporated to enhance properties such as strength, flexibility, or transparency.
Injection Molding Process
Once the mold and material are prepared, the injection molding process commences. The molten plastic is injected into the mold cavity under high pressure, filling all the intricacies of the mold.
Cooling and Ejection
After the plastic has solidified within the mold, it undergoes a cooling phase to ensure dimensional stability. Once cooled, the mold is opened, and the final product is ejected, ready for further processing or assembly.
Applications in the Medical Field
Medical Plastic Injection Molding finds extensive applications in various areas of healthcare.
Medical Devices
From catheters and syringes to implants and prosthetics, medical devices rely on precision-engineered plastic components produced through injection molding.
Surgical Instruments
Disposable and reusable surgical instruments such as forceps, scissors, and clamps are manufactured using medical plastic injection molding, ensuring sterility and durability.
Laboratory Equipment
Laboratory equipment such as test tubes, petri dishes, and pipettes are commonly made using medical-grade plastics, offering chemical resistance and precision molding.
Regulatory Compliance and Standards
The production of medical devices and components through plastic injection molding is subject to stringent regulatory requirements to ensure patient safety and product efficacy.
FDA Regulations
In the United States, the Food and Drug Administration (FDA) regulates the manufacturing, labeling, and distribution of medical devices, including those produced through injection molding.
ISO Certification
ISO standards such as ISO 13485 specify requirements for quality management systems in the design, development, production, and servicing of medical devices, ensuring compliance with international standards.
Advancements in Medical Plastic Injection Molding
Technologies and Innovations
Advancements in materials science, automation, and 3D printing have revolutionized medical plastic injection molding, allowing for greater customization, efficiency, and speed.
Future Trends
The future of medical plastic injection molding is marked by advancements in biocompatible materials, additive manufacturing, and digitalization, paving the way for personalized medicine and improved patient outcomes.
Benefits of Medical Plastic Injection Molding
Customization
Medical plastic injection molding enables the customization of components to meet the unique needs of patients and healthcare providers, leading to better treatment outcomes.
Reduced Risk of Contamination
The use of sterile and single-use plastic components reduces the risk of cross-contamination and nosocomial infections in clinical settings, enhancing patient safety.
Faster Production
Injection molding allows for high-speed production of medical components with minimal manual intervention, ensuring timely delivery and supply chain efficiency.
Challenges and Solutions
Design Complexity
The intricate designs and tight tolerances required for medical components pose challenges in mold design and production. Advanced CAD/CAM software and simulation tools help address these challenges by optimizing designs and identifying potential issues before manufacturing.
Material Compatibility
Selecting the right material with suitable properties for medical applications is crucial to ensure biocompatibility, sterilization compatibility, and regulatory compliance. Collaboration with material suppliers and rigorous testing protocols help mitigate material-related risks.
Quality Control
Maintaining consistent quality and adhering to regulatory standards throughout the manufacturing process is essential in medical plastic injection molding. Robust quality management systems, in-process inspections, and validation procedures are implemented to ensure product integrity.
Case Studies and Success Stories
[Case Study 1 Title]
[Description of case study 1]
[Case Study 2 Title]
[Description of case study 2]
Sustainability in Medical Plastic Injection Molding
Eco-friendly Practices
Efforts to reduce environmental impact in medical plastic injection molding include recycling initiatives, use of biodegradable materials, and energy-efficient manufacturing processes.
Recycling Initiatives
Recycling programs aimed at reclaiming and repurposing post-consumer medical plastics contribute to a circular economy and reduce reliance on virgin materials.
Global Market Overview
Market Size and Growth
The global market for medical plastic injection molding is witnessing steady growth driven by increasing demand for medical devices, technological advancements, and growing healthcare infrastructure worldwide.
Key Players
Leading companies in the medical plastic injection molding market include [Company 1], [Company 2], [Company 3], among others, offering a wide range of services and solutions to meet the diverse needs of the healthcare industry.
Conclusion
Medical plastic injection molding plays a pivotal role in the healthcare industry, providing precision-engineered components essential for medical devices, equipment, and instruments. With advancements in technology and materials, this manufacturing process continues to evolve, driving innovation and improving patient care.