What is the Purpose of a Medical Plastic Molding Machine?
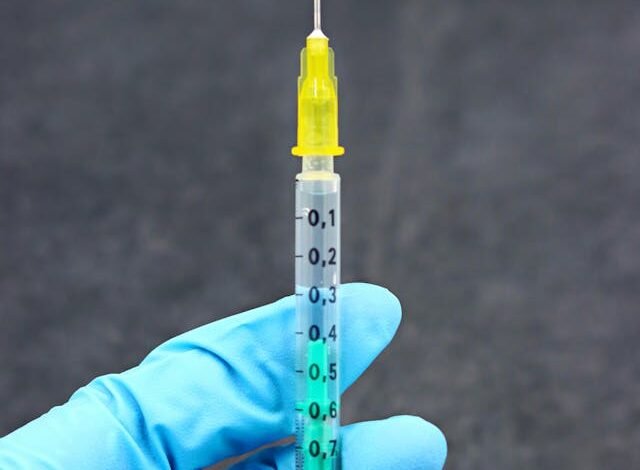
Medical plastic molding machines play a crucial role in the manufacturing of various medical devices and components. These machines utilize advanced technology to produce precise and high-quality plastic parts used in medical applications. In this article, we delve into the purpose of medical plastic molding machines, their functionality, applications, advantages, and future trends.
Introduction to Medical Plastic Molding Machines
Medical plastic molding machines are specialized equipment designed for the production of plastic parts used in the medical industry. These machines are capable of molding intricate shapes with high precision, ensuring consistency and reliability in the manufactured components.
Understanding the Purpose of Medical Plastic Molding Machines
What are Medical Plastic Molding Machines?
Medical plastic molding machines employ the process of Medical Injection Molding to create plastic parts. Injection molding involves injecting molten plastic material into a mold cavity, where it cools and solidifies to form the desired shape. These machines are equipped with precision control systems to manage temperature, pressure, and other parameters during the molding process.
The Importance of Precision in Medical Devices
Precision is paramount in the medical industry, where components must meet stringent quality standards to ensure safety and efficacy. Medical plastic molding machines enable manufacturers to achieve the level of precision required for producing critical medical devices such as syringes, catheters, implants, and diagnostic equipment.
How Medical Plastic Molding Machines Work
Injection Molding Process
The injection molding process begins with the feeding of plastic pellets into the machine’s hopper. The pellets are then heated and melted in a barrel before being injected into the mold cavity under high pressure. Once the plastic material fills the mold, it is cooled and ejected as a solid part.
Role of Temperature and Pressure Control
Temperature and pressure control are essential aspects of the injection molding process. Precise control of these parameters ensures uniformity in the molded parts and prevents defects such as warping, shrinkage, or porosity.
Key Features of Medical Plastic Molding Machines
Cleanroom Compatibility
Many medical plastic molding machines are designed to operate in cleanroom environments to prevent contamination of the manufactured components. These machines feature sealed enclosures and filtration systems to maintain cleanliness standards.
Material Selection and Compatibility
Medical plastic molding machines are compatible with a wide range of medical-grade materials, including thermoplastics, thermosets, and elastomers. Manufacturers can choose materials based on their specific requirements for biocompatibility, sterilization, and durability.
Applications of Medical Plastic Molding Machines
Manufacturing of Medical Devices and Components
Medical plastic molding machines are used to produce a diverse range of medical devices and components, including housings, connectors, tubing, and surgical instruments. These machines enable mass production of precise parts with minimal waste, contributing to cost-effectiveness and scalability.
Prototyping and Testing
In addition to mass production, medical plastic molding machines are utilized for prototyping and testing purposes. Manufacturers can quickly iterate designs and produce small batches of parts for evaluation and validation before full-scale production.
Advantages of Using Medical Plastic Molding Machines
Cost-Effectiveness
Medical plastic molding machines offer cost-effective solutions for manufacturing medical devices compared to traditional machining or fabrication methods. The automated nature of Medical Injection Molding reduces labor costs and material waste, resulting in overall savings for manufacturers.
Faster Production Cycles
Injection molding enables rapid production cycles, allowing manufacturers to meet tight deadlines and respond promptly to market demands. With high-speed and high-volume capabilities, medical plastic molding machines ensure efficient throughput and timely delivery of medical products.
Challenges and Considerations in Using Medical Plastic Molding Machines
Regulatory Compliance and Quality Assurance
Compliance with regulatory standards such as ISO 13485 and FDA requirements is essential for medical device manufacturers. Medical plastic molding machines must adhere to stringent quality control measures to ensure product safety, traceability, and documentation throughout the manufacturing process.
Maintenance and Calibration Requirements
Proper maintenance and calibration are critical for the reliable operation of medical plastic molding machines. Regular servicing and calibration ensure optimal performance, minimize downtime, and extend the lifespan of equipment. Manufacturers must establish comprehensive maintenance schedules and protocols to uphold machine integrity and product quality.
Future Trends in Medical Plastic Molding Technology
Integration of Automation and Robotics
The integration of automation and robotics is a growing trend in medical plastic molding technology. Automated systems enhance efficiency, consistency, and productivity in manufacturing operations, while robotics enable precise handling and assembly of components, further streamlining the production process.
Advancements in Material Science
Continual advancements in material science contribute to the development of innovative materials tailored for medical applications. New polymers, composites, and bioresorbable materials offer enhanced properties such as biocompatibility, strength, and flexibility, opening up new possibilities for medical device design and performance.
Conclusion
In conclusion, medical plastic molding machines serve a vital purpose in the production of medical devices and components, facilitating precision, efficiency, and cost-effectiveness in manufacturing operations. With advanced technology, strict quality control measures, and ongoing innovation, these machines play a crucial role in shaping the future of healthcare.
FAQs
- What types of medical devices can be manufactured using plastic molding machines?
- Medical plastic molding machines can produce a wide range of devices, including syringes, catheters, implants, surgical instruments, and diagnostic equipment.
- How do medical plastic molding machines ensure product quality and safety?
- Medical plastic molding machines incorporate precision control systems, cleanroom compatibility, and adherence to regulatory standards to ensure product quality and safety.
- What are the key considerations when selecting materials for medical plastic molding?
- Key considerations include biocompatibility, sterilization methods, mechanical properties, and regulatory compliance with medical device regulations.
- What maintenance practices are recommended for medical plastic molding machines?
- Regular maintenance practices include cleaning, lubrication, inspection of components, calibration of temperature and pressure settings, and monitoring of machine performance.