What is Medical Device Plastic Molding Used For?
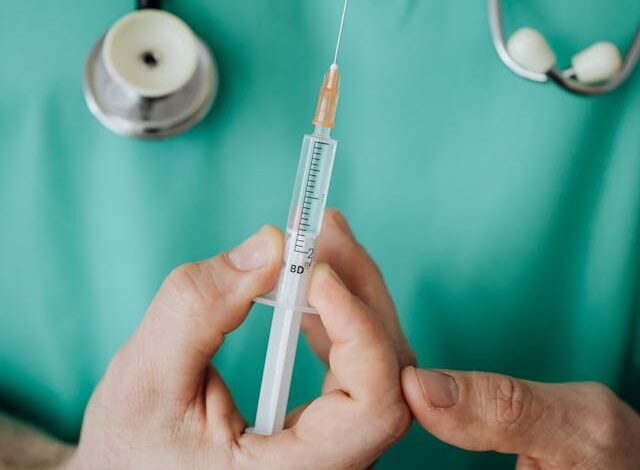
Medical device plastic molding plays a crucial role in the production of various medical instruments, implants, and equipment used in healthcare settings. This innovative manufacturing process involves shaping plastic materials into specific forms to create devices that are integral to modern medical practices. Let’s delve deeper into the significance, process, and applications of medical device plastic molding.
Introduction to Medical Device Plastic Molding
Medical device plastic molding is a manufacturing technique used to produce a wide range of medical instruments and devices made from plastic materials. These devices serve essential functions in diagnosing, treating, and monitoring medical conditions, contributing significantly to patient care and healthcare delivery.
Types of Medical Devices Produced through Plastic Molding
Implants
Implantable medical devices, such as pacemakers and joint replacements, are often manufactured using plastic molding techniques due to the durability and biocompatibility of certain polymers.
Prosthetics
Customized prosthetic limbs and orthoses can be efficiently produced through plastic molding processes, allowing for precise shaping and fitting to meet individual patient needs.
Surgical Instruments
Disposable surgical instruments, including syringes, forceps, and catheters, are commonly fabricated using plastic molding for cost-effectiveness and sterile single-use purposes.
Benefits of Using Plastic Molding for Medical Devices
Cost-effectiveness
Plastic molding offers cost-efficient production methods, making medical devices more accessible to healthcare providers and patients alike.
Customization
The flexibility of plastic molding allows for the customization of medical devices to accommodate specific patient requirements, enhancing treatment outcomes and patient satisfaction.
Durability
Plastic-molded medical devices are known for their durability and resistance to corrosion, ensuring long-term reliability and performance in clinical settings.
The Process of Medical Device Plastic Molding
Medical device plastic molding encompasses several manufacturing processes, including:
Injection Molding
Medical Injection Molding involves injecting molten plastic material into a mold cavity, where it solidifies to form the desired shape of the medical device.
Blow Molding
Blow molding is utilized to produce hollow plastic components, such as bottles and containers, by inflating a heated plastic preform inside a mold cavity.
Compression Molding
Compression molding applies pressure to a heated plastic material within a mold cavity, allowing for the production of complex-shaped medical devices with precise dimensional accuracy.
Materials Used in Medical Device Plastic Molding
The selection of materials for medical device plastic molding is critical to ensuring product quality, safety, and biocompatibility. Commonly used materials include:
Polymers
Various thermoplastics, such as polyethylene, polypropylene, and polycarbonate, are frequently employed in medical device manufacturing due to their versatility and ease of processing.
Additives
Additives, such as antimicrobial agents and radiopaque compounds, can be incorporated into plastic materials to enhance their functional properties and performance in medical applications.
Biocompatibility Considerations
Medical-grade plastics must undergo rigorous testing to ensure biocompatibility and compatibility with biological tissues and fluids, minimizing the risk of adverse reactions or complications in patients.
Regulatory Compliance and Quality Standards
The production of medical devices through plastic molding is subject to stringent regulatory requirements and quality standards, including:
FDA Regulations
The U.S. Food and Drug Administration (FDA) regulates the manufacturing, labeling, and marketing of medical devices to ensure their safety and effectiveness for patient use.
ISO Certifications
International Organization for Standardization (ISO) certifications, such as ISO 13485 for quality management systems, are essential for demonstrating compliance with global regulatory standards in medical device manufacturing.
Applications Across Medical Fields
Medical device plastic molding finds diverse applications across various medical specialties, including:
Cardiology
Innovative cardiac implants and devices, such as stents and heart valves, are produced through plastic molding techniques to address cardiovascular diseases and improve patient outcomes.
Orthopedics
Customized orthopedic implants and surgical instruments are manufactured using plastic molding processes to treat musculoskeletal conditions and injuries with precision and reliability.
Ophthalmology
Disposable contact lenses and intraocular lenses are examples of medical devices produced through plastic molding, providing vision correction and therapeutic solutions for ophthalmic disorders.
Challenges and Limitations
Despite its numerous advantages, medical device plastic molding presents certain challenges and limitations, including:
Sterilization
Ensuring the sterility of plastic-molded medical devices during production and packaging is crucial to prevent contamination and infection in clinical settings.
Material Selection
The choice of plastic materials must consider factors such as biocompatibility, mechanical properties, and sterilization compatibility to meet the specific requirements of medical applications.
Design Complexities
Designing complex medical devices for plastic molding can pose challenges related to mold design, material flow, and dimensional accuracy, requiring careful planning and optimization.
Future Trends in Medical Device Plastic Molding
The future of medical device plastic molding is characterized by ongoing technological advancements and innovative developments, including:
3D Printing Advancements
Additive manufacturing technologies, such as 3D printing, offer new possibilities for rapid prototyping and customized production of medical devices with intricate geometries and structures.
Nanotechnology Integration
The integration of nanomaterials and nanocomposites into plastic molding processes enables the development of next-generation medical devices with enhanced properties, such as antimicrobial activity and targeted drug delivery.
Sustainability Initiatives
Efforts to promote sustainability in medical device manufacturing involve the use of biodegradable polymers, recycling programs, and eco-friendly production processes to minimize environmental impact and resource consumption.
Case Studies and Success Stories
Examples of innovative medical devices produced through plastic molding include:
- Biodegradable implants for tissue regeneration
- Wearable medical sensors for remote patient monitoring
- Minimally invasive surgical tools for precision surgeries
The Impact of Medical Device Plastic Molding on Healthcare
Medical device plastic molding contributes to healthcare advancements by:
- Facilitating the development of novel medical technologies
- Improving patient outcomes and quality of life
- Streamlining healthcare delivery and reducing costs
Conclusion
In conclusion, medical device plastic molding like Medical Injection Molding is a vital manufacturing process that enables the production of a wide range of innovative medical devices used in various healthcare settings. By harnessing the capabilities of plastic materials and advanced molding techniques, medical device manufacturers can create cost-effective, customized, and durable solutions to address diverse medical needs and challenges.