What is an Injection Molding Machine?
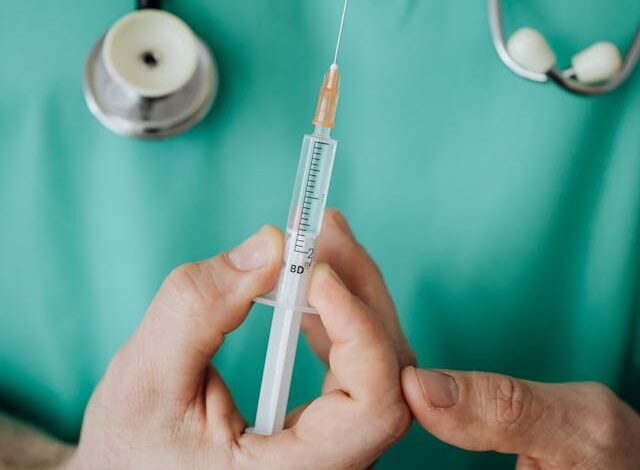
Injection molding is a pivotal process in modern manufacturing, and at the heart of this process lies the injection molding machine. Let’s delve into what exactly an injection molding machine is, how it works, its components, applications, advantages, and the future of this technology.
Introduction
Injection molding machines are industrial Medical Molding machines utilized to produce parts by injecting molten material into a mold. This process is highly versatile and is extensively used across various industries due to its efficiency and precision.
History of Injection Molding Machines
Injection molding machines have a rich history dating back to the late 19th century. Early developments primarily focused on rubber molding, but over time, advancements in technology led to the evolution of plastic injection molding machines.
Components of Injection Molding Machine
An injection molding machine consists of several key components, including the injection unit, clamping unit, and mold. Each component plays a crucial role in the injection molding process.
Injection Unit
The injection unit is responsible for melting and injecting the material into the mold. It comprises a hopper, barrel, and screw assembly, where the material is heated and then forced into the mold cavity.
Clamping Unit
The clamping unit holds the mold in place during the injection process. It applies the necessary pressure to keep the mold closed while the material is injected and cooled.
Mold
The mold defines the shape and structure of the final product. It consists of two halves, the cavity, and the core, which are precisely machined to produce the desired part.
Working Principle of Injection Molding Machine
The injection molding process typically involves three main phases: injection, clamping, and cooling/ejection.
Injection Phase
During this phase, the material is heated and injected into the mold under high pressure.
Clamping Phase
The mold is securely closed, and the material is allowed to cool and solidify within the mold cavity.
Cooling and Ejection Phase
Once the material has cooled and solidified, the mold opens, and the finished part is ejected from the machine.
Types of Injection Molding Machines
There are several types of injection molding machines available, including hydraulic, electric, and hybrid machines, each with its own unique advantages and applications.
Hydraulic Injection Molding Machines
These machines use hydraulic power to generate the necessary pressure for injection.
Electric Injection Molding Machines
Electric machines utilize electric motors for injection and are known for their precision and energy efficiency.
Hybrid Injection Molding Machines
Combining the benefits of hydraulic and electric machines, hybrid machines offer improved efficiency and performance.
Applications of Injection Molding Machines
Injection molding machines find widespread use across various industries, including automotive, consumer goods, and medical sectors, due to their ability to produce high-quality, complex parts with ease.
Advantages of Injection Molding Machines
Injection molding offers numerous advantages over traditional manufacturing methods, including high efficiency, cost-effectiveness, and versatility in design.
Challenges and Limitations
Despite its advantages, injection molding also poses certain challenges, such as high initial setup costs, material selection constraints, and maintenance requirements.
Future Trends in Injection Molding Technology
The future of injection molding technology in Medical Molding industry is poised for advancements in Industry 4.0 integration, enabling smarter, more efficient manufacturing processes, along with a focus on sustainable practices to minimize environmental impact.
Conclusion
Injection molding machines play a vital role in modern manufacturing, offering unparalleled efficiency, precision, and versatility. With ongoing advancements in technology and materials, the future of injection molding looks promising, catering to diverse industry needs while embracing sustainability.