Maximizing Efficiency with Predictive Maintenance
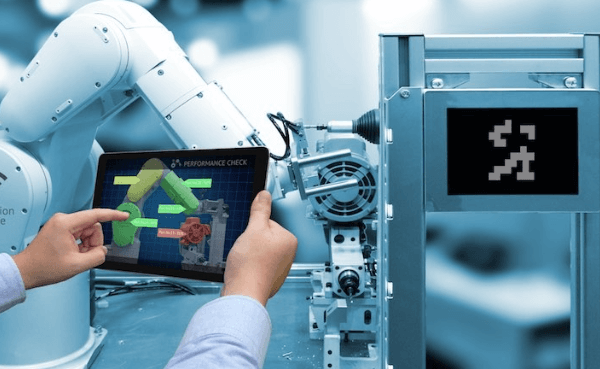
The modern industrial world is changing quickly, making dependable and efficient machinery more important than ever.Downtime, unexpected failures, and maintenance costs can significantly impact a company’s bottom line, leading to the development and adoption of innovative maintenance strategies. Among these strategies, predictive maintenance has emerged as a powerful tool for optimizing equipment performance and minimizing disruptions. This article delves into what predictive maintenance is, how it works, and the benefits it brings to various industries.
Understanding Predictive Maintenance
Predictive maintenance is a proactive approach to equipment maintenance that uses data analysis and real-time monitoring to predict when a machine or system is likely to fail. Unlike traditional maintenance methods, which are either reactive (fixing equipment after it breaks) or preventive (regularly scheduled maintenance regardless of equipment condition), predictive maintenance seeks to anticipate issues before they lead to failure.
The core idea behind predictive maintenance is to collect data from sensors embedded in machinery. These sensors monitor various parameters such as vibration, temperature, pressure, and oil levels. The data collected is then analyzed using advanced algorithms, machine learning models, and historical maintenance records to identify patterns and trends. By doing so, predictive maintenance systems can forecast when a component is likely to fail or when performance is beginning to degrade. This allows maintenance teams to address potential problems before they cause downtime, ensuring that equipment runs smoothly and efficiently.
See also: Exploring Pigging Design: Optimizing Pipeline Performance
How Predictive Maintenance Works
Implementing predictive maintenance involves several key steps, each crucial to accurately predicting equipment failures and optimizing maintenance schedules.
Data Collection: The ongoing gathering of machine data is the cornerstone of predictive maintenance.Sensors play a vital role in this process, gathering information on various operational parameters in real time. These sensors are strategically placed on equipment to monitor specific components that are prone to wear and tear. For example, vibration sensors can detect imbalances in rotating machinery, while temperature sensors can identify overheating issues in electrical components.
Data Analysis: Once the data is collected, it is processed and analyzed using advanced analytics tools. This step involves the application of machine learning algorithms that can detect anomalies, identify patterns, and predict potential failures. The data analysis phase is critical because it transforms raw data into actionable insights. For instance, by analyzing vibration data over time, the system can identify a pattern that indicates a bearing is beginning to wear out, allowing maintenance teams to schedule a replacement before the bearing fails.
Predictive Modeling: Predictive modeling is the process of using historical data, along with real-time sensor data, to create models that predict when equipment is likely to fail. These models are continuously refined and updated as new data is collected, improving their accuracy over time. Predictive models can be tailored to specific types of equipment or components, providing highly targeted predictions that help maintenance teams focus their efforts where they are most needed.
Maintenance Scheduling: Based on the insights provided by predictive models, maintenance teams can develop optimized maintenance schedules. Instead of relying on fixed maintenance intervals, which may be too frequent or not frequent enough, predictive maintenance allows for maintenance to be performed precisely when it is needed. This reduces unnecessary maintenance activities, extends the life of components, and minimizes the risk of unexpected failures.
Benefits of Predictive Maintenance
The adoption of predictive maintenance offers numerous benefits that can significantly enhance the efficiency and reliability of industrial operations. These benefits include cost savings, reduced downtime, and improved asset lifespan.
Cost Savings: One of the most significant advantages of predictive maintenance is its potential to reduce maintenance costs. By predicting when a component is likely to fail, maintenance teams can intervene before a failure occurs, avoiding the high costs associated with emergency repairs and unplanned downtime. Additionally, predictive maintenance can reduce the frequency of routine maintenance activities, saving both time and resources.
Reduced Downtime: Unplanned downtime can be costly, leading to lost production, missed deadlines, and dissatisfied customers. Predictive maintenance helps minimize downtime by identifying potential issues before they escalate into full-blown failures. By addressing problems early, maintenance teams can schedule repairs during planned maintenance windows, ensuring that production continues uninterrupted.
Improved Asset Lifespan: Predictive maintenance not only prevents failures but also helps extend the lifespan of equipment. By monitoring the condition of components in real time, maintenance teams can ensure that machinery is operating within optimal parameters. This proactive approach reduces the stress and wear on equipment, leading to longer lifespans and a better return on investment.
Enhanced Safety: Equipment failures can pose significant safety risks, especially in industries such as manufacturing, energy, and transportation. Predictive maintenance reduces the likelihood of catastrophic failures that could endanger workers or lead to environmental hazards. By maintaining equipment in good working order, companies can create a safer working environment and comply with safety regulations.
Data-Driven Decision-Making: Predictive maintenance provides maintenance teams with valuable data that can inform decision-making processes. For example, by analyzing maintenance data over time, companies can identify recurring issues, evaluate the effectiveness of different maintenance strategies, and make informed decisions about equipment upgrades or replacements. This data-driven approach leads to more effective maintenance practices and better overall asset management.
Predictive Maintenance in Practice
Predictive maintenance is being implemented across a wide range of industries, each benefiting from the technology in different ways.
Manufacturing: In the manufacturing industry, predictive maintenance is used to monitor production machinery, such as CNC machines, conveyors, and robotics. By predicting when these machines are likely to fail, manufacturers can avoid costly downtime and maintain high levels of productivity. Additionally, predictive maintenance helps manufacturers optimize their maintenance schedules, reducing the frequency of maintenance activities and minimizing disruptions to production.
Energy and Utilities: The energy and utilities sector relies heavily on predictive maintenance to ensure the reliability of critical infrastructure. Power plants, wind turbines, and transmission lines are equipped with sensors that monitor their condition in real time. Predictive maintenance allows energy companies to address potential issues before they lead to power outages or equipment failures, ensuring a steady and reliable supply of energy to customers.
Transportation: In the transportation industry, predictive maintenance is used to monitor vehicles, aircraft, and trains. By predicting when critical components such as engines, brakes, or landing gear are likely to fail, transportation companies can perform maintenance before failures occur, reducing the risk of accidents and improving the reliability of their fleets. Predictive maintenance also helps transportation companies optimize their maintenance schedules, reducing the time vehicles spend out of service.
Oil and Gas: The oil and gas industry operates in some of the most challenging environments, where equipment failures can have severe consequences. Predictive maintenance is used to monitor drilling rigs, pipelines, and refineries, helping companies identify potential issues before they lead to costly downtime or environmental disasters. By maintaining equipment in optimal condition, oil and gas companies can improve the safety and efficiency of their operations.
Challenges of Implementing Predictive Maintenance
While predictive maintenance offers numerous benefits, implementing it can be challenging. Companies must overcome several hurdles to fully realize the potential of this technology.
Initial Investment: The upfront cost of implementing predictive maintenance can be significant, especially for small and medium-sized enterprises. Companies must invest in sensors, data analytics tools, and the necessary infrastructure to support predictive maintenance. However, the long-term benefits, such as reduced maintenance costs and improved asset reliability, often outweigh the initial investment.
Data Management: Predictive maintenance generates vast amounts of data, which must be collected, stored, and analyzed. Managing this data effectively requires robust data management systems and skilled personnel who can interpret the data and make informed decisions. Companies must invest in the necessary tools and training to ensure that their predictive maintenance programs are successful.
Integration with Existing Systems: Integrating predictive maintenance with existing maintenance management systems can be challenging. Companies must ensure that their predictive maintenance tools are compatible with their existing systems and processes. This may require significant changes to workflows and the adoption of new technologies.
Conclusion
Predictive maintenance is transforming the way companies manage their assets, offering a proactive approach to maintenance that reduces costs, minimizes downtime, and extends the lifespan of equipment. By leveraging data analytics and real-time monitoring, predictive maintenance enables companies to predict when equipment is likely to fail, allowing them to address issues before they lead to costly disruptions. While implementing predictive maintenance can be challenging, the benefits it offers make it a valuable tool for any industry that relies on the efficient and reliable operation of machinery. As technology continues to evolve, predictive maintenance will play an increasingly important role in helping companies stay competitive in a rapidly changing world.