Electron Beam Drilling: A Precision Technique
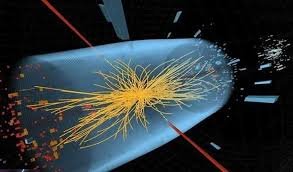
Precision and Automation come in handy in advanced manufacturing and engineering. Revolutionized the industry EBD is proving to be the solution with incredible micro-hole creation capabilities at high speeds. In the following article, I will discuss the principles, applications, and advantages of Electron Beam Drilling and also spread light on other drilling techniques and why Electron Beam Drilling is different from other drilling techniques.
What is Electron Beam Drilling?
Electron Beam Drilling is a method by which a focused beam of high-speed electrons is bombarded against the surface of a material, generating heat at the point of impact. Heated this way it can melt or vaporize the material to form a hole. EBD, in contrast to mechanical drilling which utilizes mechanical abrasion, is a non-contact method, therefore it is well-suited for soft or heat-sensitive materials.
It goes back to the mid-20th century initially driven by aerospace and defense sectors with their requirements for miniaturization and extreme accuracy. Since then Electron Beam Drilling has been used in the medical, automotive, and electronics industries that required fine holes, complex patterns, and repeatable precision.
How Does Electron Beam Drilling Work?
The heart of EBD technology is the electron beam, a highway of electrons that blast through a vacuum environment at highly accelerated speeds and become focused to an extremely small point on the target metal. Let me outline the process for you:
- ELECTRON GENERATION: The filament of electron gun is heated to release electrons through thermionic emission.
- Electron Acceleration and Focusing: The electrons get accelerated in a high-voltage field and later go through magnetic lenses that help focus them into a beam.
- Beam-Target Interaction: Upon arrival of the electron beam onto the surface of the material, heat is delivered in an extremely short time period, resulting in localized melting or vaporization depending on beam intensity.
- Drilling and Precision Control: By controlling the position, strength, and duration of the beam, EBD allows the creation of holes with micron-level precision, making EBD a useful tool for micro-drilling.
It is this process of precise heating and drilling that gives Electron Beam the edge over thin or complicated materials that could warp or degrade with traditional means.
Advantages of Electron Beam Drilling
High accuracy and repeatability
First things first, Electron Beam Drilling is capable of making holes as small as a few microns in diameter with very high reproducibility and is therefore key in applications requiring precise tolerances. Mechanical drilling, especially in the case of some very hard or brittle materials, is not capable of achieving this level of accuracy.
Non-Contact Process
EBD is based on a contactless working principle which emerges basically no hard wear on tools thereby obtaining a longer service life with minimum tool replacement frequency. This advantage leads to less maintenance and an extended service time for the drill rig.
Compatibility with a Range of Materials
The method is compatible with different kinds of materials metal, ceramics and composites. EBD can drill materials that are difficult to machine using conventional methods, for example, tungsten, titanium or stainless steel.
Drilling Various Complicated Parts
The specialized hole patterns and complex geometries that are possible with Electron Beam Drilling are often not achievable with mechanical drilling. This is especially important in applications such as turbine blades, fuel injector nozzles, and other parts which require complex geometries to work properly.
Environmentally Friendly
Since it doesn’t require cutting fluids or lubricants, EBD is an environmentally cleaner option compared to traditional drilling. Additionally, the absence of tool wear means that less waste is generated over time.
Applications of Electron Beam Drilling
Electron Beam Drilling is widely used in industries where precision and complexity are essential. Some of its most common applications include:
Aerospace
The aerospace industry was among first to adopt EBD for components that require high precision and strength. For instance, EBD is used to drill cooling holes in turbine blades and vanes, helping to improve their thermal efficiency and longevity.
Medical Devices
Electron Beam Drilling has become imperative for medical device manufacturing, including complex designs like catheters, needles, and stents. Drilling precision holes as small as 0.05 mm helps ensure these devices function properly and safely.
Automotive and Electronics
As automotive components become increasingly complex, EBD offers an effective solution for producing fine holes in fuel injectors and microchips. It enables high-speed production with consistent quality, crucial for mass production in the automotive and electronics sectors.
Energy
In the energy industry, components such as fuel nozzles and high-performance filtration systems require precise and complex hole patterns that EBD can provide. This precision enhances fuel efficiency, reduces emissions, and improves overall system performance.
Comparisons with Other Drilling Methods
Electron Beam Drilling isn’t only precision-drilling technology available. Other methods include laser drilling, electrical discharge machining (EDM), and ultrasonic drilling. Here’s how EBD compares:
- Laser Drilling: While laser drilling also uses energy to remove material, it may lack the precision and depth control of EBD. EBD offers tighter tolerances and can drill deeper holes with greater accuracy.
- EDM (Electrical Discharge Machining): Utilizing sparks to melt material away, EDM is effective only with conductive material, limiting its applicability range. EBD, in contrast, is compatible with all materials even non-conductives.
- Ultrasonic Drilling: Ultrasonic methods are typically slower and more suited for softer materials, making them less ideal for the hard metals or composites that EBD can handle with ease.
Each method has its strengths, but Electron Beam Drilling provides unmatched accuracy and material versatility, making it the preferred choice for applications requiring extreme precision.
Challenges and Considerations in Electron Beam Drilling
While EBD offers numerous advantages, it’s essential to consider its limitations and operational requirements:
Vacuum Environment
Since electrons are easily scattered by air molecules, EBD requires a high-vacuum environment, which can add to the operational costs and complexity.
Initial Setup Costs
Electron Beam Drilling equipment is more expensive than traditional mechanical drills. However, the increased efficiency and reduced maintenance costs often justify the investment in the long term.
Training and Expertise
Operating EBD machinery requires specialized training, as technicians must understand intricacies of electron beam manipulation and vacuum technology.
Despite these challenges, the benefits of Electron Beam Drilling, particularly in high-value, precision-oriented industries, far outweigh its limitations.
The Future of Electron Beam Drilling
Advancements in future will only make Electron Beam Drilling more accurate, affordable, and widely employed. Already, new innovations in beam control, automation, and digital interfacing are on the horizon, making the EBD an even more capable choice, and appealing to an even broader range of industries. The other area of research is damping down EBD with other processes such as laser drilling to develop hybrid technologies that may allow multi-functional machines to accommodate more diverse manufacturing needs.
In addition, with industries calling for greener practices, the green side of EBD such as near-zero waste and lower requirement of cutting fluids will potentially be a selling point.
Conclusion
In contemporary manufacturing, Electron Beam Drilling is one of most important techniques that allows for the precise and efficient drilling of complex patterns and micro-holes in materials that are difficult to machine. The value of this process, ranging from high accuracy to material versatility, makes it desirable across aerospace, medical, automotive, and energy sectors. EBD has its own set of requirements–vacuum environment, high setup cost, etc but, the benefit achieved through EBD definitely compensates for the cost incurred, especially in industries where precision and reliability are of utmost importance.
For more detailed insights into Electron Beam Drilling technology, visit Electron Beam Drilling to learn how this groundbreaking method continues to shape the future of precision manufacturing.