Different Types of Sheet Metal Bending
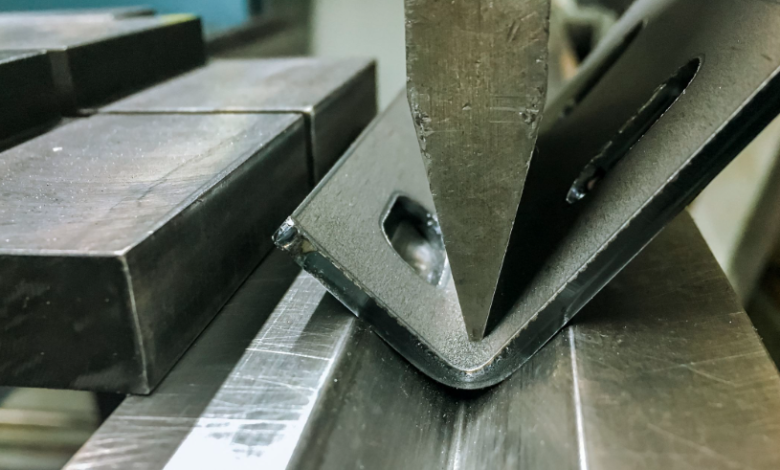
Sheet metal bending is an essential process in metal fabrication, used to shape metal sheets into specific angles and forms without cutting or removing material. This method is widely applied in industries like automotive, aerospace, construction, and manufacturing, enabling the production of strong, durable, and precisely shaped components.
There are several Types of Sheet Metal Bending each designed for different applications, materials, and precision levels. Understanding these bending methods helps manufacturers choose the right technique for their specific requirements. This article explores the most common types of sheet metal bending, their working principles, applications, advantages, and challenges.
What is Sheet Metal Bending?
Sheet metal bending is a cold-forming process where force is applied to a metal sheet to bend it along a straight axis. The metal does not lose its thickness but undergoes deformation to achieve the desired shape. The bending process is performed using tools like press brakes, dies, rollers, and punches to create different angles, curves, or channels.
Depending on the bending requirements, various techniques are used to achieve precise results. The selection of the bending method depends on factors such as material type, thickness, bend angle, and production volume.
Common Types of Sheet Metal Bending
Several methods are used in sheet metal bending, each with distinct characteristics and applications. The most widely used bending techniques include:
1. V-Bending
V-bending is the most common type of sheet metal bending, performed using a V-shaped die and a punch. The metal sheet is placed over the die while the punch presses it into the desired angle.
Types of V-Bending:
- Air Bending: The punch does not press the sheet fully into the die, allowing flexibility in bend angles. This method requires less force and is suitable for various materials.
- Bottoming: The sheet is fully pressed into the die, achieving a precise bend angle with minimal springback. It is ideal for high-accuracy applications.
- Coining: High pressure is applied to imprint the punch and die shape onto the metal, ensuring extremely accurate bends with almost no springback.
Applications of V-Bending:
- Automotive body panels
- Aerospace structures
- Metal brackets and frames
2. U-Bending
U-bending is similar to V-bending but uses a U-shaped die instead of a V-die. This method is used to form curved bends that are commonly required in tubing, pipes, and enclosures.
Applications of U-Bending:
- Pipe fittings
- Structural supports
- Metal housings and enclosures
3. Roll Bending
Roll bending involves passing a metal sheet through a set of rotating rollers to gradually bend it into curved or cylindrical shapes. It is commonly used for large-radius bends in thick sheets.
Read also: These are the benefits of outsourcing license management for businesses
Applications of Roll Bending:
- Manufacturing of tanks and cylinders
- Large metal pipe production
- Curved metal structures in construction
4. Edge Bending (Flanging)
In edge bending, the sheet metal is clamped at one end while force is applied to the opposite side to bend the edge. This method is often used to create flanges or reinforced edges.
Applications of Edge Bending:
- Sheet metal panels with reinforced edges
- Electrical enclosures
- Automotive body parts
5. Rotary Bending
Rotary bending uses a specially designed rotary tool to bend the sheet metal while minimizing surface damage. This technique is suitable for aesthetic applications where surface finish is critical.
Applications of Rotary Bending:
- High-quality appliance casings
- Decorative metal components
- Precision-formed metal parts
6. Wipe Bending
Wipe bending involves placing the metal sheet over a wiping die while a punch forces it down to create a bend. This method is used when sharp, accurate bends with minimal springback are required.
Applications of Wipe Bending:
- Sheet metal doors and panels
- Custom brackets
- Electronics enclosures
7. Step Bending
Step bending, also known as bump bending, is a technique where multiple small bends are made in succession to create a gradual curve. This is used for large-radius bends when roll bending is not feasible.
Applications of Step Bending:
- Aerospace components
- Large structural metal parts
- Custom metal designs
8. Hemming
Hemming involves folding the edge of a sheet metal part onto itself to create a smooth, reinforced edge. This process is used to eliminate sharp edges and improve safety.
Applications of Hemming:
- Automotive doors and hoods
- Metal furniture edges
- Decorative metal parts
9. Curling
Curling is a bending method where the sheet metal is rolled into a loop or circular shape. This is done to remove sharp edges and add strength to the sheet.
Applications of Curling:
- Safety edges on sheet metal components
- Automotive trims
- Aerospace panels
Factors Affecting Sheet Metal Bending
The success of any sheet metal bending process depends on several factors that influence the accuracy and quality of the final product.
1. Material Type
Different metals have unique bending properties. Aluminum, stainless steel, copper, and mild steel all require different bending techniques due to variations in ductility and hardness.
2. Sheet Thickness
Thicker sheets require higher force and more specialized equipment to bend without cracking or deforming.
3. Bend Radius
The bend radius is the inner curve of the bend. A smaller bend radius increases the risk of cracking, while a larger radius ensures a smoother bend.
4. Springback Effect
After bending, metal sheets tend to partially return to their original shape due to elasticity. This effect is countered by overbending or using precise bending techniques like coining.
5. Grain Direction
The internal grain structure of metal sheets affects bending. Bending across the grain results in better flexibility and reduces the risk of cracks.
Advantages of Different Types of Sheet Metal Bending
Each type of sheet metal bending offers specific benefits depending on the application:
- V-Bending and U-Bending – Ideal for precise angles and structural components.
- Roll Bending – Best for creating curved or cylindrical shapes.
- Rotary and Wipe Bending – Ensures smooth finishes for aesthetic applications.
- Hemming and Curling – Provides reinforced edges for safety and durability.
Challenges in Sheet Metal Bending
While sheet metal bending is widely used, certain challenges must be considered:
- Springback issues can affect bend accuracy.
- Material cracking can occur with improper bend radii.
- Tool wear and maintenance increase production costs.
- Limited bending for thick sheets requires specialized equipment.
Conclusion
Understanding the different types of sheet metal bending is crucial for selecting the right process based on application requirements, material properties, and design specifications. From V-bending and roll bending to hemming and curling, each method plays a key role in modern manufacturing. By leveraging advanced bending techniques and automation, industries can achieve higher precision, efficiency, and product quality while minimizing material waste.