CNC Machining: Precision and Efficiency in Modern Manufacturing
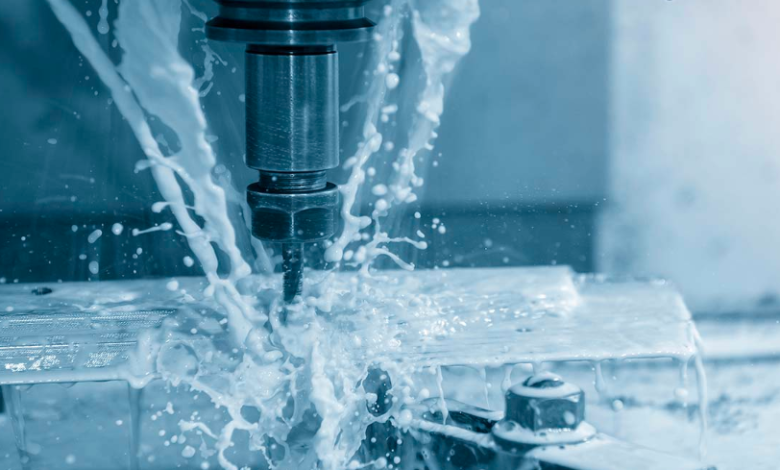
CNC machining has revolutionized the way industries produce complex and precise components. From aerospace to medical and automotive sectors, this advanced manufacturing technique ensures high accuracy, consistency, and efficiency. By utilizing computerized controls, CNC machining enhances productivity and minimizes errors, making it an essential part of modern production processes.
This article explores the fundamentals of CNC machining, its advantages, applications, and how it compares to traditional machining methods.
Understanding CNC Machining
CNC (Computer Numerical Control) machining is a manufacturing process that uses computerized systems to control machine tools. Unlike manual machining, which requires human operation, CNC machining automates cutting, milling, drilling, and shaping processes with extreme precision. A pre-programmed design is fed into the CNC system, which directs the machine to produce components according to exact specifications.
The process begins with CAD (Computer-Aided Design) software, where engineers create digital blueprints of the required part. This design is then converted into machine-readable instructions using CAM (Computer-Aided Manufacturing) software. The CNC machine follows these instructions, shaping raw materials such as metal, plastic, or composites into finished products with high accuracy.
Key Advantages of CNC Machining
1. Unmatched Precision
CNC machines operate with micrometer-level accuracy, ensuring that each part meets the specified dimensions without variations. This precision is critical in industries like aerospace and medical, where even minor deviations can lead to failures.
2. Improved Efficiency and Speed
Automation eliminates the need for constant human supervision, allowing CNC machines to run 24/7. This leads to faster production cycles, reduced lead times, and increased overall efficiency.
3. Cost-Effectiveness
While the initial investment in CNC machines may be high, the long-term savings are significant. Automation reduces labor costs, minimizes material waste, and enhances productivity, making CNC machining a cost-effective solution.
4. Consistency and Repeatability
CNC machining ensures that every product is identical, making it ideal for mass production. Unlike manual machining, where human error can lead to inconsistencies CNC machining delivers uniform results every time.
5. Versatility in Material Processing
CNC machines can work with a wide range of materials, including metals (aluminum, steel, titanium), plastics, ceramics, and composites. This versatility allows industries to manufacture a variety of products using a single CNC system.
Common Applications of CNC Machining
1. Aerospace Industry
The aerospace sector requires highly precise and durable components. CNC machining is used to manufacture aircraft parts such as turbine blades, structural panels, and engine components, ensuring safety and performance.
2. Automotive Industry
CNC machining plays a crucial role in producing vehicle components, including engine blocks, transmission parts, and suspension systems. Its ability to maintain tight tolerances ensures the reliability of automotive parts.
3. Medical Industry
Precision is vital in medical device manufacturing. CNC machining produces surgical instruments, implants, prosthetics, and diagnostic equipment with high accuracy, ensuring patient safety and treatment effectiveness.
4. Electronics Industry
The miniaturization of electronic components demands extreme precision. CNC machining helps produce circuit boards, heat sinks, and enclosures for electronic devices, ensuring optimal functionality.
5. Defense and Military Sector
The defense industry requires robust and precise equipment. CNC machining is used to manufacture weapon components, military vehicles, and communication systems, ensuring durability and reliability in critical applications.
CNC Machining vs. Traditional Machining
While traditional machining has been a cornerstone of manufacturing for decades, CNC machining offers numerous advantages over manual methods.
Feature | CNC Machining | Traditional Machining |
Accuracy | High (micrometer-level precision) | Moderate |
Automation | Fully automated | Manual operation |
Efficiency | Fast and continuous | Slower, requires breaks |
Complexity | Handles intricate designs | Limited capabilities |
Consistency | Identical parts every time | Prone to human error |
CNC machining’s ability to handle complex designs, automate processes, and maintain consistency makes it the preferred choice for modern manufacturing.
Choosing the Right CNC Machining Service
Selecting the right CNC machining service provider is crucial for ensuring high-quality production. Here are some factors to consider:
1. Experience and Reputation
A well-established CNC machining company with a proven track record ensures reliability and expertise in handling various projects.
2. Material Capabilities
Different industries require different materials. Ensure that the CNC service provider can work with the specific materials needed for your project.
3. Quality Assurance
A good CNC machining service should have stringent quality control measures to guarantee accuracy and durability in every product.
4. Production Capacity
Whether you need small batches or large-scale production, the CNC provider should have the capacity to meet your demand without compromising quality.
5. Customization and Flexibility
The ability to modify designs and accommodate special requests is essential for industries requiring unique or customized components.
The Future of CNC Machining
As technology advances, CNC machining continues to evolve. Some of the key trends shaping the future of CNC machining include:
1. Artificial Intelligence and Machine Learning
AI-powered CNC machines can optimize cutting paths, predict maintenance needs, and improve efficiency through real-time data analysis.
2. 5-Axis CNC Machining
Traditional CNC machines operate on three axes (X, Y, and Z). 5-axis CNC machining enables greater flexibility, allowing for the creation of more complex geometries with fewer setups.
3. Internet of Things (IoT) Integration
IoT-connected CNC machines provide real-time monitoring, allowing manufacturers to track production efficiency, detect faults, and improve operational workflows.
4. Sustainable Manufacturing
With increasing environmental concerns, CNC machining is becoming more eco-friendly. Reduced material waste, energy-efficient machines, and recycling initiatives contribute to sustainable manufacturing practices.
Conclusion
CNC machining has transformed the manufacturing industry by offering precision, efficiency, and cost-effectiveness. Its applications span across various sectors, from aerospace and automotive to medical and electronics. With continuous advancements in technology, CNC machining is set to become even more powerful and versatile in the future.
By understanding the benefits and capabilities of CNC machining, businesses can make informed decisions to improve production quality, reduce costs, and stay competitive in the modern industrial landscape.