From SMT to PCBA Test: The Path to a Successful Assembly Process
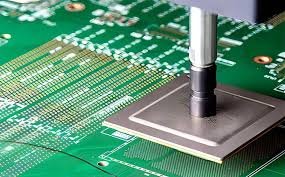
There are many tactics for electronics. Every step is crucial to ensure the last product plays nicely and lasts a long time. The manner begins with Surface Mount Technology (SMT) and ends with Printed Circuit Board Assembly (PCBA) trying out.
In this text, we can explain the basic steps of the meeting procedure in easy-to-apprehend terms. You will see how these steps are uploaded to reliable circuit boards.
What is SMT?
We can see that smt meaning Surface Mount Technology (SMT) is a way of attaching minor electronic additives to a circuit board. These small parts are known as floor mount devices (SMDs).
Previously, digital components have been inserted into the holes within the frames, but SMT has changed that method because it is quicker and higher.
Why is SMT Important?
Smaller gadgets: SMT makes devices smaller, lighter, and smaller, including smartphones or clever watches.
Fast manufacturing: Machines can deploy many small components quickly, saving time.
Improved performance: SMT reduces the distance between components, making the system greener and faster.
Steps in the Assembly Process
The route from SMT to PCBA test checking out consists of numerous key steps. Let’s go through them one at a time.
1. To practice solder paste
The manner starts offevolved by using spraying the board with solder paste. Solder paste is like glue that holds small parts collectively and helps with electrical connections.
A stencil is positioned on the board to show where the paste goes.
The paste is located where the components can be saved.
Why is this step critical? Proper use of solder paste guarantees that all elements adhere well and characteristic as they must.
2. Installation of substances
After using the solder and paste, the SMT elements are located on the panel.
The choose-and-vicinity machines set up every component quickly and appropriately.
These gadgets work correctly, even in minimal packages.
Why is this step vital? Proper placement of the parts is crucial for the board to function well.
3. Reflow soldering
After that, the tune returns to the waft oven. This furnace heats the solder paste until it melts, creating a decent bond between the elements and the board.
Once heated, the panel cools, and the solder hardens, locking the components in an area.
Why is this step crucial? Reflow soldering guarantees that each component is firmly connected and equipped for use.
4. Research
After soldering, the panel is checked for defects.
Automated Optical Inspection (AOI): Mechanical inspection for lacking, mismatched, or broken components.
X-ray evaluation: For complex boards, X-rays have a look at hidden areas, inclusive of in-chip connections.
Why is this step vital? The inspections capture issues early and store time and money later.
5. Addition of Through Holes
Some elements, such as connectors, should be inserted into the holes inside the panel. This is known as a through-hollow meeting.
These parts are mainly synthetic and are made by hand or machine.
Why is this step necessary? Through-hole assemblies provide extra power for parts coping with flowing water or physical stresses.
6. Testing the PCBA
Several checks should be carried out to ensure proper operation before the board is ready.
In-Circuit Testing (ICT): This tests if all connections and additives are operating as designed.
Functional testing: The board is tested in a way that determines how it’ll feature within the very last product.
Why is this step crucial? Testing guarantees that the board is reliable and prepared to be used in real-world programs.
Challenges in the Process
While machines manage the maximum of the paintings, there may be challenges:
Harmful elements: Small parts can shift at some stage in the meeting, inflicting issues.
Solder troubles: Too a good deal or too little solder paste can cause awful connections.
Detecting bugs at some stage in trying out: Bugs observed overdue within the manner can be costly to restore.
Addressing these challenges early enables create a clean procedure.
Benefits of a right series machine
If each step is achieved efficiently, the assembly manner offers many benefits:
High: The final product plays appropriately and lasts a long term.
Efficiency: Automation hurries up the process and reduces mistakes.
Reliability: Testing ensures that the product meets consumer expectations.
Cost savings: Fewer errors suggest less money and time spent on repairs.
Tips for achievement
Follow those pointers to make sure a a hit assembly.
Use the best materials: High-nice solder paste and additives distinguish considerably.
Invest in the system: Reliable machinery for accuracy and speed.
Train personnel: Experienced employees can spot problems early and save them.
Follow standards: Use industry guidelines to ensure safety and reliability.
conclusion
From making use of solder paste to checking out PCBAs, each step of the assembly process is essential. SMT allows for smaller, quicker, and more efficient designs; at the same time, checking out ensures that the product operates nicely earlier than it reaches the consumer.
By knowing the stairs and avoiding unusual mistakes, producers can create high-quality electronics. This procedure now not most effective improves the effectiveness of the product but additionally builds consumer self belief.